Educational Series: A Closer Look at Leather
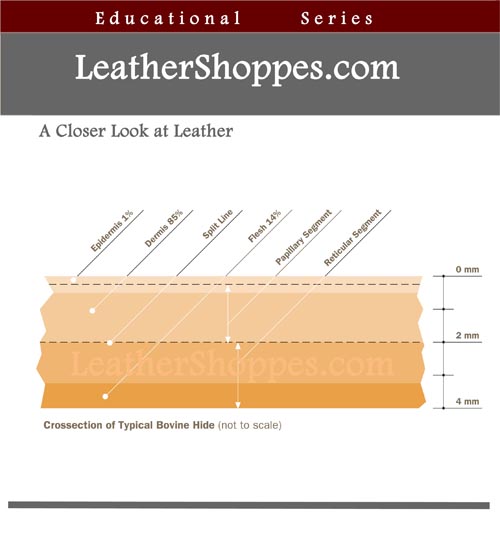
Enlarge Diagram
When leather hides are split, the bottom segment of the hide is sold to tanners who process suede or reticular leather.
The fiber structure is the tighest at the uppermost layer of the hide. Leather commonly referred to as "top grain" have the epidermis and the upper portion of the hide removed by sanding or buffing, resulting in products which have lost the ability to breathe because they are heavily pigmented with finish applications which color the surface, protect the leather and mask natural imperfections.
Full top grain leather
Full top grain leather would be the outer most area of the hide where the hair was, but not altered in any way by buffing or sanding. This would be considered the best quality leather hide available.
Top grain leather
Top grain leather is the outmost area of the hide, but an addiitional step in the processing, the top part is sanded or buffed to minimize naturally occurring imperfections.
BiCast leather
Bicast leather (also known as bi-cast leather, bycast leather or PU leather, sometimes described as split leather) is a material made with a split leather backing covered with a layer of polyurethane (hence the term PU leather) that is applied to the surface and then embossed.
Bonded leather (not real leather)
Bonded leather is made by shredding leather scraps and leather fiber, then mixing it with bonding materials. The mixture is extruded onto a fiber cloth, or paper backing, and the surface is usually embossed with a leather-like texture or grain. Color and patterning, if any, are a surface treatment that does not penetrate like a dyeing process would.
The natural leather fiber content of bonded leather varies. The manufacturing process is somewhat similar to the production of paper. Generally a leather content of any where from 10-25% is used as a backing for bonded leather. Lower-quality materials may suffer flaking of the surface material in as little as a few years, while better varieties are considered very durable and retain their pattern and color even during commercial use.
Because the composition of bonded leathers and related products varies considerably (and sometimes is a trade secret), it may be difficult to predict how a given product will perform over the course of time. There is a wide range in the longevity of bonded leathers and related products; some better-quality bonded leathers are claimed to be superior in durability over low-quality genuine leather. Generally Bonded leathers have a much lower warranty time period associated with them.
Disadvantages:
- Difficult or impossible to repair or recondition after wear or damage
- Outgassing and "sweating" of plasticizers and other chemicals from poorly-formulated products is possible
Possible Advantages:
- Cost savings to consumer, usually less expensive then top grain leather
- Product consistency – no natural defects and minimal batch to batch variation
- High cutting yield – cost efficient and reduces waste, similar to fabric
- High durability and flame retardancy (for some formulations)
- Extensive design options – from leather effects to bold geometric designs